Start-up Byways: no more waiting at loading docks
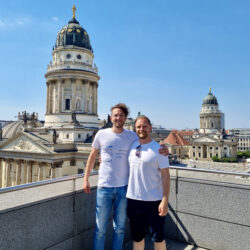
Founded in 2020, Byways has developed a pragmatic tool that allows trucks and warehouses to better align their logistics operations. This has already led to a reduction in waiting time of more than 45% for customers, according to co-founder Alexander Palffy.
Anyone who has ever visited a large distribution centre knows what it is like: a swarm of trucks delivering or collecting goods. For all parties involved, this is a costly source of inefficiency. Drivers have to wait for a dock to become available, warehouse staff unnecessarily stand by for a truck that eventually arrives late, and planners are rushed off their feet with phone calls and apps trying to keep everything on track. This is what German supply chain start-up Byways wants to put an end to. With its solution for dynamic time slot & yard management, loading and unloading should become a fluid operation, with no more waiting.
Existing solutions too rigid
Byways was founded in Berlin in 2020 by two young entrepreneurs. “We saw a strong need for a logistics solution that matched the dynamics of the sector. Traditional solutions were too rigid for this,” says Palffy, who has been familiar with a warehouse environment since his high-school days and worked for a digital freight forwarder, among others. In the photo, he can be seen standing arm-in-arm with his associate Simon Jordan (right), who has a PhD in Machine Learning and was employed by Volkswagen Research for eight years. “Our goal was to develop a user-friendly platform that would be easy to implement and would eliminate all the hassle of emails and phone calls.”
Implementation in 30 minutes
The solution Byways conceived and developed is a planning tool, a dashboard and a communication platform all in one. Trucks from suppliers, customers and logistics providers can be easily connected to it and are in direct contact with the logistics hubs. Planners see on their dashboards where delays occur, have direct contact with drivers and can quickly rebook a time slot. “Our system stands out from other yard management systems because of the simplicity of implementation,” says Palffy. “This can be done within half an hour and familiarization is very quick. Furthermore, the system can be tailored to any industry, any type of warehouse and takes driver language into account.”
No more calls and emails
The Berlin-based company is already quite successful. It employs 32 people and has more than a thousand customers, including fashion retailer Asos, construction supplier Cemex and logistics provider GXO Logistics. “We have customers in the top 10 largest logistics companies in the world,” Palffy says with a hint of pride. He is equally proud of the results customers are achieving with his tool. “We see a demonstrable decrease of more than 45% in the time trucks and loading docks have to wait for each other. Furthermore, we see an increase in planning efficiency by more than 30%. Companies no longer need to call or email to organize their consignments.”