Supply chain digital twin helps Intel and La-Z-Boy to respond faster
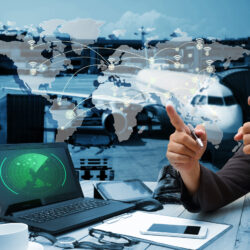
In view of the steady stream of supply chain disruptions, there is a rapidly growing need for fast scenario analysis. What should be done if a production line grinds to a halt or a distribution centre is forced to close? Or if there is a sudden surge or drop in demand? More and more companies are developing their own supply chain modelling skills. During a recent Webinar Wednesday, AIMMS explained how companies such as Intel and La-Z-Boy are benefiting from a digital twin of their supply chain.
By Marcel te Lindert
What should we do now? Will we need extra production capacity to prevent unacceptably long delivery times? And what would be the best location for an additional production facility? Those were just a few of the many questions American furniture manufacturer La-Z-Boy faced when consumers suddenly started buying more armchairs and sofas at the start of the COVID-19 pandemic and the market demand seemed to be growing exponentially overnight.
The 94-year-old company from Monroe, near Detroit, found answers to those questions by analysing various scenarios using software from AIMMS, which specializes in supply chain modelling. “They started by building a model of their existing supply chain. That’s always the first step,” said Aanan Panday, Supply Chain Consultant at AIMMS. “Above all, a model of the existing supply chain makes it possible to validate the example using historical data. This is necessary to gain confidence in the design. In addition, a model of the existing supply chain is needed to find out whether a modification will actually result in an improvement.”
Tens of millions
The second step consists of drawing up several what-if scenarios. What if La-Z-Boy were to increase the capacity of its existing factories? What if it were to open a completely new production plant? Analysis of various scenarios using the model slowly produced a reliable picture of the optimal supply chain design. “The entire process took several months, but as a result they knew exactly which production locations did or didn’t require extra capacity,” added Panday.
But this was not a one-off exercise for La-Z-Boy. Now that the company has a reliable modelling tool at its disposal, it uses it to gain insight into solutions to new supply chain challenges and uncertainties. As a result, new ideas about supply chain design can be analysed relatively quickly and easily. “This has enabled them to save tens of millions of euros in costs,” stated Panday.
From a model to a digital twin
COVID-19 has greatly increased the need for supply chain modelling at companies like La-Z-Boy. Before the pandemic, supply chains operated in relatively stable and predictable times. As long as those supply chains were running smoothly, COOs preferred to leave them be. But when the first lockdowns were imposed, many companies turned to modelling to be able to adapt their supply chains quickly. With the problems still continuing – and even being exacerbated by new disruptions such as the war in Ukraine – scenario analysis has become the order of the day.
Panday: “Once you have a good model based on current data – let’s call it a digital twin – then you can change a few parameters and immediately see what the supply chain impact will be. This continuously facilitates the right trade-offs between costs, risks, product availability and sustainability.”
Tactical and operational questions
The nature of the questions themselves has changed too. Previously, supply chain modelling was an annual exercise to answer strategic questions relating to the optimal production and distribution locations. Nowadays, it is used for tactical and operational questions, such as how much manufacturing capacity and inventory do I need at each location? And which products should I manufacture first, or store close to the front of my warehouse?
Modelling the supply chain has become a lot easier thanks to tools like those from AIMMS. You still need a data analyst who knows where the necessary data is, how to make that data usable and how to update it. “In addition, you need operational knowledge: how the supply chain processes work, and what are – and are not – realistic scenarios. At La-Z-Boy, all that knowledge and experience was combined in one person, but you usually need two or three people for that. And they are commonly able to produce the first results within a few months,” said Panday.
Lockdown in Shanghai
Computer chip manufacturer Intel decided to set up its own supply chain modelling team when the company was forced to close some distribution centres during the lockdown and had to act quickly in order to maintain its service to customers. The firm subsequently felt the need to take renewed action when a worldwide chip shortage loomed. “Intel had a number of questions: What can we do to reduce delivery times and increase chip availability? And what is the best way to ship the orders, given the rising costs and risks? These were all difficult questions in view of the supply chain complexity,” explained Paul van Nierop, Product Owner at AIMMS.
Once a digital twin of the supply chain had been built using the AIMMS tool, it quickly proved to be of great value. Van Nierop: “Take the recent lockdown in the city of Shanghai, which had a major impact on Intel’s distribution centre there. In a single session, Intel was able to analyse various scenarios: What if we have to close the distribution centre? Where should we store our products then? And how will that impact on our costs and delivery times? That exercise helped Intel to realize that it can use its digital twin not only reactively, but also proactively for contingency planning purposes so that people immediately know what to do if something like this happens to them again.”