Locus Robotics opens European headquarters in Amsterdam
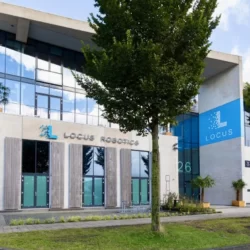
Locus Robotics, a supplier of warehouse robots, has opened its first office outside the USA in northern Amsterdam. During the official opening ceremony, CEO Rick Faulk described the current situation as a perfect storm for robotics suppliers: “There’s a worker shortage, labour costs are high, demand for e-commerce is growing and companies need to deliver ever faster.” In the demo area at the new head office, employees showed visitors what makes the company’s robots so special and how they can double a human order picker’s productivity.
By Harm Beerens
Locus supplies what are known as collaborative robots or ‘cobots’. Rather than being machines that can replace employees, they provide support so that existing staff can work more efficiently. Warehouse operatives no longer have to trundle the picking carts up and down the aisles, but can instead stay in one zone while the cobots fetch any items required from other zones. In the demo area of the new facility, the self-propelled picking carts could be seen whizzing past the racks autonomously, stopping if necessary to give way to each other and any visitors. When they arrive at a picking spot, the waiting operative checks the cobot’s screen to see which product has to be picked, scans it and places it in the relevant crate on the cobot. After this has been confirmed by tapping the tablet, the robot whizzes off again on its way to the next zone. In the meantime, the next cobot has arrived with picking instructions for the operative.
Doubling productivity
Locus Robotics has customers all over the world, but especially in countries where there is a labour shortage and/or where labour costs are relatively high. In Europe, its robots are used by companies such as Geodis, Ceva, DHL and the British drugstore chain Boots. “On average, our solution increases the productivity of a warehouse operative by a factor of two,” claimed Faulk (pictured) during his speech. “To achieve that result, you need about three cobots for every human employee.” The investment is quickly recouped in the shape of higher profit, particularly in countries with high labour costs, but he explained that there are other benefits too: “Cobots make working in a warehouse less demanding and therefore more appealing to people. And it’s safer, because robots drive around a warehouse more carefully than people do, and they also cause less damage.”
Robots-as-a-Service
During the demonstration of the cobots, visitors were asked if they wanted to pick a few orders themselves. It turned out to be amazingly easy. The robot guided itself to the right location, and the tablet provided clear instructions with an image and the code of the product to be picked. Faulk looked on in satisfaction as a journalist gave it a try and got it right first time. “In an e-commerce environment, you often have to deal with peaks in the workload so you need to be able to rapidly scale up capacity. Staff turnover is also relatively high. So it’s handy that it’s so easy to work with our robots because it means you can train people up quickly,” he commented.
But doesn’t temporarily scaling up also mean that you need extra robots? “Yes, which is why we certainly don’t advise customers to actually purchase our robots,” said Faulk. ‘We strongly believe in the Robotics-as-a-Service model based on looking at how many robots you need for each period, such as per month. Adding an extra robot is literally just a matter of taking it out of the box, uploading the warehouse floorplan and then setting to work. We chose this model not only because it’s better aligned with the market needs, but also because it’s sustainable. We take care of the necessary maintenance on the robots and they receive all updates automatically. When they reach the end of their life cycle, they are completely overhauled so that they can be deployed again elsewhere.”