Tesla gears up Gigafactory for launch of Model 3
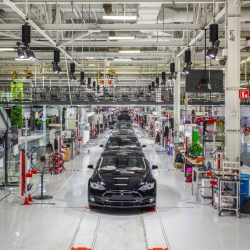
Tesla’s mission to produce sufficient electric vehicles to force change in the automobile industry is accentuating its focus on lithium ion battery production. With planned production of at least 500,000 cars by the end of decade and the already high demand for the Tesla Model 3 there are simply not enough batteries worldwide to suffice. To fill the gap Tesla started construction of its Gigafactory in Sparks, Nevada, USA in 2014 in cooperation with Panasonic for the manufacture of battery cells for its cars and other energy products.
By Helen Armstrong
The Gigafactory is expected to be fully operational by 2020 when it will be the world’s largest producer of lithium ion batteries and is expected to employ around 10,000 people. In the meantime production of its 2170 battery cell has already started and Tesla CEO Elon Musk says it is the world’s highest and cheapest energy density cell.
The first cells will be used for the company’s Powerwall 2 and Powerpack 2 energy products with battery production for Model 3 starting later this year, ahead of the car’s volume production expected by the end of the year.
Model 3, which is designed to have an affordable entry price of 35,0000 US dollars, will be manufactured at the company’s Fremont factory in California. It currently produces some 100,000 cars. While Tesla is scaling-up production at Fremont it recently announced that electric motors and gear boxes for Model 3 will also take place at the Gigafactory.
The Gigafactory so called because of its target annual battery production capacity of 35 gigawatt-hours (GWh), was orginally intended for battery only production. However, Tesla could eventually vertically integrate the entire production process within one plant – at least for ‘Gigafactory 2’ which it is planning to build in Europe. Musk has said it is reinventing its manufacturing strategy now referred to as “the machine that builds the machine” and recently acquired Germany’s Grohmann Engineering, a specialist in high tech automated production systems, to support the transition.
Peter Carlsson who was responsible for supply chain management during the launch of Tesla’s first electric cars, Model S and Model X, is confident that the supply chain for the new model will be easier. Although he left the company in 2015 he told Automotive News that Tesla has resolved some issues through internal vertical integration.
He explained that during the early years the company had no history of volumes and had to build relationships with suppliers. Also while the Fremont manufacturing site for Model S was chosen for its proximity to engineering expertise, it was further from the automotive supply clusters. Although he still feels it was the right choice it did add logistics costs and complexity, he said.
“The volumes of the Model 3 will be more attractive, and I think we will see more suppliers relocate,” Carlsson told the publisher.
After Musk announced that Gigafactory 2, would be build in Europe, politicians from France, Germany, the Netherlands, Portugal and Czech Republic to name but a few, have been courting the Tesla top man. The business will ensure thousands of jobs from one of the world’s most acclaimed companies. The location of Gigafactory 2 is likely to be announced later this year.