Cost no longer only priority in supply chain design
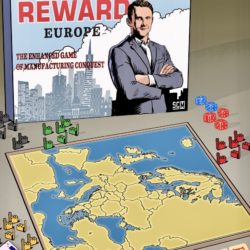
The shift in manufacturing from west to east has noticeably slowed. A production base in a low-wage country is no longer the be-all and end-all. Other factors have become more important in supply chain network design, such as flexibility, responsiveness and resilience. Besides that, it is becoming increasingly difficult to find a country with a stable political climate.
By Marcel te Lindert
Prins Castings & Forgings has been active in China for more than 20 years, because that’s where the major producers are based of the metallurgical products that Prins supplies to customers throughout Europe. Those customers include a large number of machinery and equipment builders. Many of their products are based on sheets of metal that have been cut and bent into the right shape before being welded and subsequently assembled.
Prins has an in-house engineering and design department that translates the requirements for construction parts into casting and forging needs. “This is a more cost-effective approach because it eliminates all the process steps such as cutting, bending, welding and assembly of the individual parts. Besides that, castings often look nicer and are lighter – and weight is a very important factor for builders of transport vehicles,” says Marcel Pot, CEO of Prins.
Prins has not only a network of suppliers in China, but also its own offices which maintain contact with the manufacturers and safeguard the product quality, including by auditing the production processes. “In addition, we have our own logistics & testing facility. All the products are sent there first so that we can thoroughly test and check them. Needless to say, nothing is shipped to Europe unless it passes the quality control tests. Once a container arrives in Rotterdam, it is transported to our distribution centre in Amersfoort. From there, we ship the right products to our customers at the right time,” explains Pot.
Best-cost countries
The low wages in China were one of the reasons for choosing that country, but it doesn’t mean that Prins produces all its order in China. “We work with manufacturers all over the world, including in Spain, France, Italy and the Czech Republic. We think very carefully about which orders should be produced where, and especially in the case of more complex forgings and castings. Whenever we receive an order, we shortlist two or three producers who we believe are capable of supplying the right product quality. We request a proposal from all of them, and then we place the order with whoever offers us the best terms and conditions. That’s sometimes a European supplier.”
Pot prefers to call them ‘best-cost countries’ rather than ‘low-cost countries’. Forging and casting is a labour-intensive process, and the unit cost is undeniably lower in China than in the Czech Republic, for example. “But it’s the quality that’s important. The producer in China might make a hundred castings, of which only 80 are any good. In that case it’s cheaper to work with a Czech supplier who will produce 99 usable units.”
Lead time is rarely an issue; it takes five weeks for a container to travel from China to Amersfoort. “Our standard lead time is four to five months, including production time. Yes, that’s long, but it’s hardly ever a reason for us to choose a European supplier. When we do opt for production in Europe, it’s almost always because of the higher quality standards. We get the castings produced in large batches and hold them in stock in Amersfoort, remember, so we can often deliver quickly to our customers across Europe.” … … …
Want to read more?
Subscribe to the digital subscription to read the full version >>
or
select one of our annual or digital subscriptions to receive the next issue >>
This article was first published in Supply Chain Movement 35 | Q4 – 2019